Unser umfangreiches Robotersortiment bietet neben anwendungsbezogenen Varianten wie Schweiss-, Palettier-, Lackier- und Handling-Roboter auch Modelle für Labor- und Reinraumapplikationen sowie schlüsselfertige automatisierte Schweißsysteme höchster Qualität.
Bearbeitungszentren und Teilereinigung komplett automatisiert - mit Robotern gegen den Personalmangel
Bei einem führenden Anbieter von Produkten und Lösungen für Sanitär, Heizungs- und Kühlungsanlagen in Landau in der Pfalz automatisieren Yaskawa-Roboter Bearbeitungszentren samt angeschlossener Teilereinigungsanlage. Das Robotik-Vorzeigeprojekt ist die perfekte Lösung für unter Personalmangel leidende Unternehmen und bietet gleichzeitig eine Reihe weiterer Vorteile.
Die Watts Industries Deutschland GmbH ist die deutsche Tochter des weltweit agierenden und in den Vereinigten Staaten gegründeten Unternehmens Watts Water Technologies, das in 2022 weltweit mit mehr als 4.500 Beschäftigten einen Umsatz von rund zwei Milliarden US-Dollar machte. Mehr als 170 attraktive Arbeitsplätze befinden sich am Standort Landau in der Pfalz. Hier produziert das Unternehmen vorwiegend innovative Produkte für wasserführende Heizungs- und Klimaanlagen.
Was auffällt beim Vor-Ort-Besuch ist die hohe Fertigungstiefe. Entsprechend gut ausgestattet ist die Produktion. Bearbeitungsmaschinen aller Art arbeiten hier im Schichtbetrieb, darunter auch mehrere baugleiche Bearbeitungszentren von Alzmetall, die die spangebende Bearbeitung unterschiedlich langer Rohre übernehmen, die später als Verteilsysteme für Fußbodenheizungen dienen.
Über zehn Jahre lang war das Be- und Entladen dieser Bearbeitungszentren Aufgabe angelernter Mitarbeiter, die diesen Job in Mehrmaschinenbedienung ausführten. Warum das Unternehmen dennoch dringend in die Automatisierung dieser Maschinen investieren musste, bringt Andreas Becker, Industrial Engineer bei Watts Industries, auf den Punkt: „Wir leiden hier am Standort massiv unter Personalmangel. Um den kontinuierlichen Betrieb der Maschinen im Schichtbetrieb sicherzustellen, blieb nur die Investition in Roboter. Dieser Schritt eröffnete die Möglichkeit, die frei werdenden Mitarbeiter an den Maschinen für höherrangige Aufgaben zu qualifizieren und sie von dem täglichen Kontakt mit Kühlschmierstoffen, den die Be- und Entladetätigkeit zwangsläufig mit sich bringt, zu entlasten.“
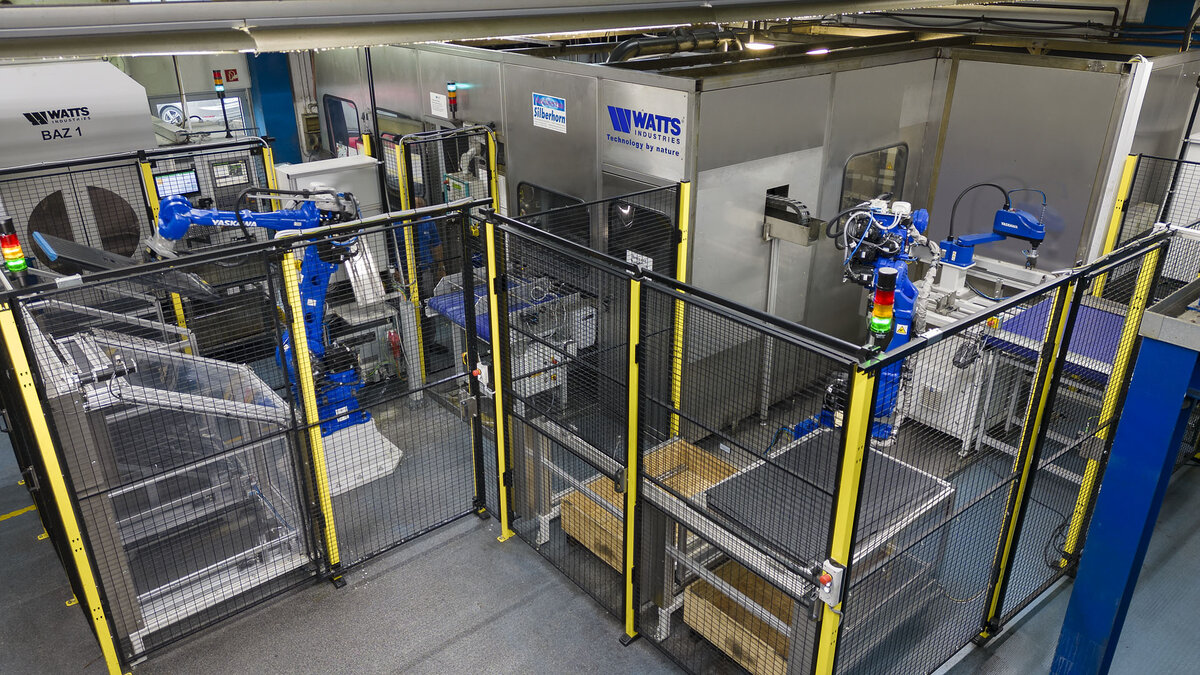
Anspruchsvolles Projekt durchgängig mit Yaskawa-Robotern automatisiert
Doch das Vorhaben, die Maschinen sowie die angeschlossene Teilereinigungsanlage zu automatisieren, ging mit großen Herausforderungen einher. Heiko Röhrig, Vertriebsleiter der mit dem Projekt beauftragen EGS Automation GmbH, erinnert sich: „Die Automatisierung von Werkzeugmaschinen mit Yaskawa-Robotern ist für uns Standard. Bei Watts sah die Sache aber anders aus. Hier bereitete uns nicht nur das stark eingeschränkte Platzangebot in der Fertigung Kopfzerbrechen, sondern auch die mit hohen Toleranzen versehene Bereitstellung der Teile in Werkstückträgerwagen.“
Bei diesen Wagen handelt es sich um Schweißkonstruktionen aus Blech, die, da nie für die Automation vorgesehen, größere fertigungstechnische Toleranzen aufweisen können. Auf einem Wagen finden – übereinander gestapelt und schräg gestellt – bis zu 15 Werkstückträger mit bis zu 48 Teilen Platz. Die Wagen werden manuell an definierter Position an der Anlage aufgegeben und verriegelt.
Um die Toleranzen der Wagen für die präzise Roboterhandhabung auszugleichen, hat sich EGS Automation eine überzeugende Lösung einfallen lassen: So ist jeder Yaskawa-Sechsachser vom Typ MOTOMAN GP50 mit einem gegen Kühlschmierstoffe resistenten Sensor am Greifwerkzeug ausgestattet, mit dem der Roboter mehrere definierte Positionen anfährt und daraus einen Korrekturfaktor für das aktuelle Koordinatensystem ermittelt. Ist die tatsächliche Stapelhöhe samt eventuell vorhandener Verkippung ermittelt, startet die eigentliche Challenge für den Roboter.
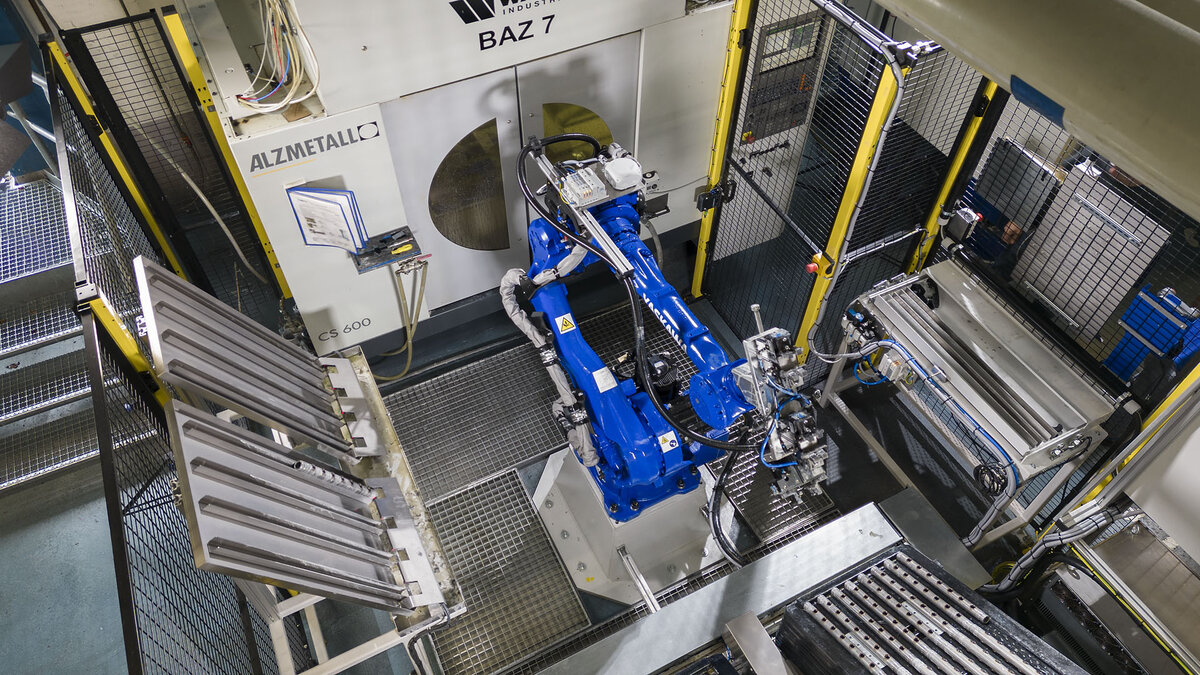
Vier Rohre in simultaner Bearbeitung
Sobald sich die Türen des Bearbeitungszentrums öffnen, zählt jede Sekunde. Der große Yaskawa-Sechsachser fährt zügig in den Arbeitsraum der Maschine, entnimmt mit seinem Doppelgreifer zwei der insgesamt vier bearbeiteten Rohre und legt sie auf einer Zwischenablage ab. Dort holt er sich zwei unbearbeitete Teile, legt sie in die Maschine ein, entnimmt im gleichen Arbeitsgang das letzte bearbeitete Paar aus der Maschine und belädt sie mit dem zweiten unbearbeiteten Teilepaar. Dann raus aus der Maschine, Türe zu und weiter geht´s mit der Bearbeitung von jeweils vier Rohren in einer Aufspannung.
Erst nach erfolgter Be- und Entladung erschließt sich, warum der Motoman GP50 mit einem weiteren Einzelgreifer ausgestattet ist. Dazu Heiko Röhrig: „Die Rohre erreichen die Anlage in dicht gepackten Kunststoffblistern, die die gleichzeitige Entnahme von zwei Rohren mit dem Doppelgreifer nicht zulassen. Da wir während der Hauptzeit der Maschine ausreichend Zeit haben, lassen wir den GP50 die Rohre Teil für Teil auf eine Zwischenablage in doppelgreifertauglichem Abstand vereinzeln. Von dort aus kann der Sechsachser die Rohre paarweise handhaben, was die Be- und Entladezeit an der Maschine signifikant reduziert.“
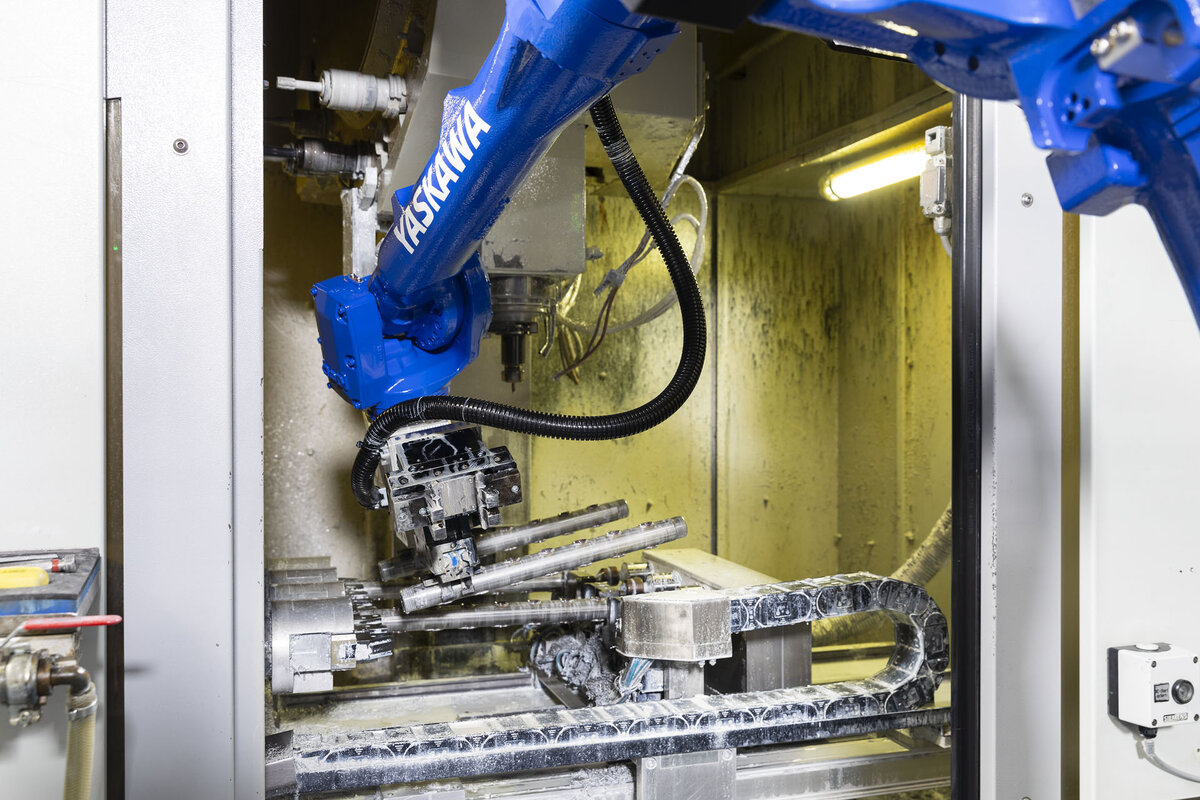
Rechnerische Programmierung statt Teachen von Varianten
Rohrrohlinge in verschiedenen Längen von 120 mm bis 750 mm, in zwei unterschiedlichen Durchmessern sowie wahlweise in Messing oder Edelstahl lassen die Variantenanzahl bereits heute auf über 50 steigen. „Um den großen Aufwand für das Teachen der zahlreichen Varianten zu vermeiden, setzen wir auf ein rein rechnerisch aufgebautes Programm. Hier gibt der Bediener selbst für neu hinzukommende Varianten nur bestimmte Parameter wie Rohrlänge, Bohrungsabstand etc. ein, und das Programm erledigt den Rest. Teachaufwand wird somit komplett vermieden“, so Heiko Röhrig.
Zu den weiteren wesentlichen Zielen bei der Automatisierung zählen eine möglichst hohe Autonomie, kurze Rüstzeiten und maximale Flexibilität. Das Konzept der Anlage, bei dem von einem Rohteil- in einen Fertigteilwagen gearbeitet wird – den Wechsel der jeweiligen Werkstückträger übernimmt der Motoman GP50 mit einer speziellen Funktion seines Doppelgreifers – lässt keine Wünsche offen: Die Flexibilität der Bearbeitungszentren in Kombination mit der Variabilität der robotergestützten Automation ermöglicht die Fertigung vieler Varianten und relativ kleiner Losgrößen in beispielloser Wirtschaftlichkeit.
Bei der Entscheidung für den richtigen Roboter hat sich Watts auf die Kompetenz des Anlagenbauers EGS Automation verlassen und dies nie bereut, wie Andreas Becker versichert: „Der Motoman GP50 von Yaskawa bietet genügend Reserven hinsichtlich Traglast und Reichweite, um auch für künftige Applikationen gerüstet zu sein. Außerdem gewährleistet sein wasserdichtes Handgelenk hundertprozentige Ausfallsicherheit auch bei intensiver Beaufschlagung mit Kühlschmierstoffen und: Die sechste Achse ist so schlank gehalten, dass wir auch unter den beengten Platzverhältnissen im Arbeitsraum der Maschine bestens zurechtkommen.“
Roboter automatisieren anschließende Teilereinigung
Ist ein Werkstückträgerwagen komplett mit bearbeiteten Teilen bestückt, entnimmt ihn ein Bediener und transportiert ihn zur Teilereinigungsanlage, die mit Yaskawa-Vier- und -Sechsachsrobotern der Typen SG650 und MOTOMAN GP50 automatisiert ist. Um eine höhere Autonomie zu gewährleisten, stehen insgesamt drei Wagenplätze zur Verfügung, wobei der Roboter Zugriff auf zwei Plätze hat. Der dritte Platz dient ausschließlich dem Bediener zum Wechseln der Wagen. Diese Lösung gewährleistet einen unterbrechungsfreien Automatikbetrieb.
Bei der Durchlaufreinigungsanlage ist die Schmutz- von der Sauberseite getrennt. Die Beladung mit den ungereinigten Rohren übernimmt ein GP50, der sie auf einem Zuführband ablegt. Nach absolviertem Bürst-, Entgrat- und Reinigungsdurchlauf verlassen die Teile die Anlage auf der Sauberseite auf einer Förderstrecke.
Hier übernimmt ein schneller Yaskawa-Scara SG650 die Handhabung der Teile. Mit höchster Dynamik legt er die Rohre in eine Station ein, in der sie über einen Lasersensor rotatorisch anhand der Bohrungen ausgerichtet werden. Im letzten Arbeitsschritt greift ein weiterer GP50 die Rohre und legt sie für den Weitertransport lageorientiert in Holzboxen ab. Um eine möglichst hohe Packungsdichte in den Boxen zu erreichen, hat EGS Automation einen Spezialgreifer entwickelt, der die Rohre nicht am Umfang, sondern in ihren Radialbohrungen greift und sie so dicht an dicht platzieren kann.
Die übergeordneten Ziele, die mit der Automatisierung einhergingen, darunter eine gewisse Unabhängigkeit gegenüber dem Personalmangel, eine höhere Produktivität, eine verbesserte Autarkie und nicht zuletzt die Schaffung eines sauberen Arbeitsumfelds für die Beschäftigten ohne Hautkontakt mit Kühlschmierstoffen ließen sich in vollem Umfang realisieren.
Und noch etwas begeistert Andreas Becker: „Das Projektmanagement von EGS Automation erwies sich als überaus verlässlich. Zeit- und Kostenkalkulationen wurden penibel eingehalten und das selbst unter erschwerten Bedingungen der Covid-Pandemie. Als ebenso zuverlässig erweisen sich die Yaskawa-Roboter, die bei der Belegschaft schnell zu geschätzten Kollegen wurden, da sie sich sehr einfach bedienen lassen und ungeliebte Aufgaben übernehmen.“
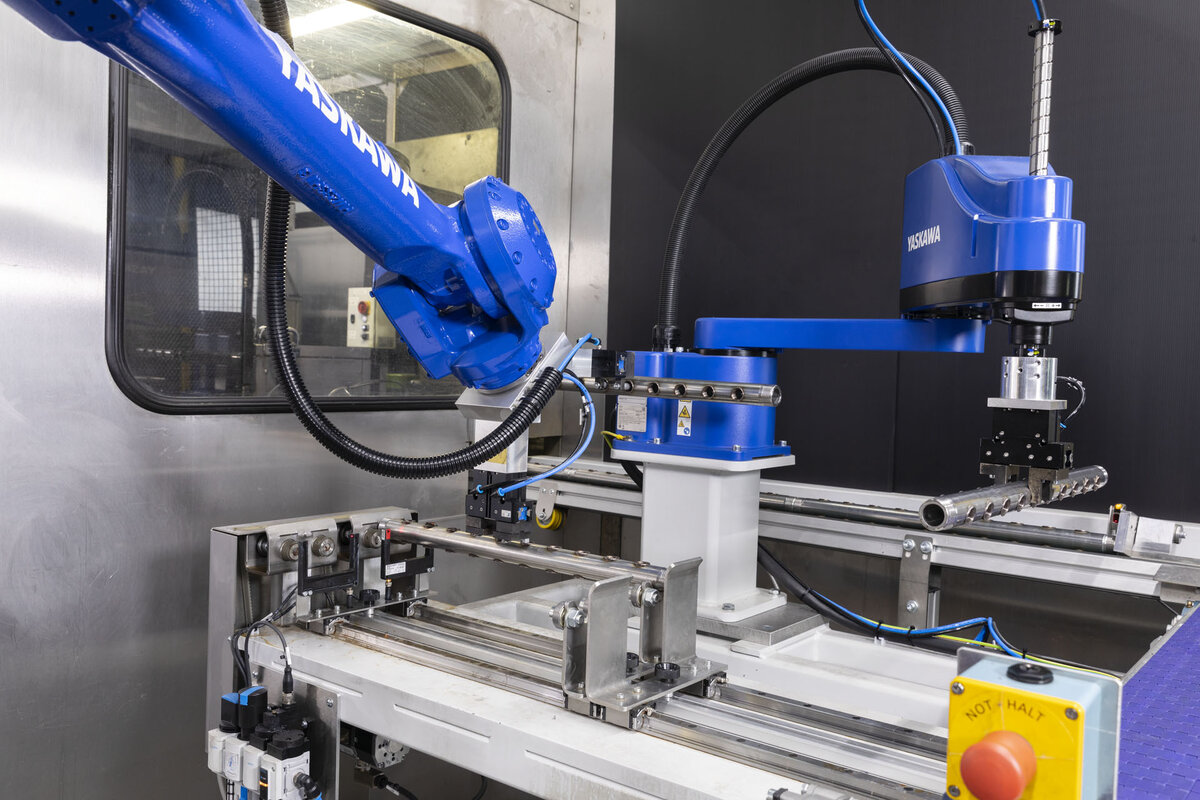
Text: Ralf Högel
Kontakt für Leseranfragen:
Yaskawa Europe GmbH
Tel. +49-8166-90-0
robotics@yaskawa.eu
www.yaskawa.de