Unser umfangreiches Robotersortiment bietet neben anwendungsbezogenen Varianten wie Schweiss-, Palettier-, Lackier- und Handling-Roboter auch Modelle für Labor- und Reinraumapplikationen sowie schlüsselfertige automatisierte Schweißsysteme höchster Qualität.
Innovantia® brings the benefits of Industry 4.0 to the ONCE production centre with 24 Yaskawa MOTOMAN robots
The Spanish National Organisation for the Blind (ONCE), as a social lottery operator of recognised prestige subject to strict public control, is one of the most dynamic and respected non-profit organisations both nationally and internationally. Since its establishment in 1938, it has been dedicated to promoting the visibility and defending the rights of people with blindness and disabilities, making its social responsibility tangible in the management of lotteries as a source of funding, always respecting principles of quality, security, transparency and trust with respect to consumers and society in general. These principles are applied in all processes of design, production, communication and marketing of lottery products, and guarantee and support their integrity in terms of accountability, security and authenticity. In line with these principles, ONCE embarked on a project to robotise its Logistics and Production Centre, implementing a new, more environmentally friendly and sustainable robotic management system to distribute to the 36,000 points of sale throughout Spain, ensuring individual processing and complete traceability from printing to delivery.
This centre coordinates, from Madrid, the distribution of all the lottery products and consumables received by ONCE points of sale throughout Spain, increasingly modernising the technical and human resources to achieve safe and responsible products, not only for people, but also for the environment. This high level of production is possible thanks to the advanced technology of the facilities, which are divided into three main areas: the printing area for traditional coupons (between 16 and 25 million coupons a week); the collection, custody and storage area for instant lotteries, with more than 450 million tickets; and the area for consumables, such as point-of-sale terminal rolls, and others. The three come together in the final process in a large Preparation Unit, a huge warehouse equipped with robots and the latest technology. These more than 44 robots, with their more than 400 automated systems, are in charge of putting together the final package, adding the products that will reach all the points of sale in individual suitcases for each salesperson. All the robots are located in a 1,500-metre warehouse, making it the space with the most robots per square metre in the Community of Madrid.
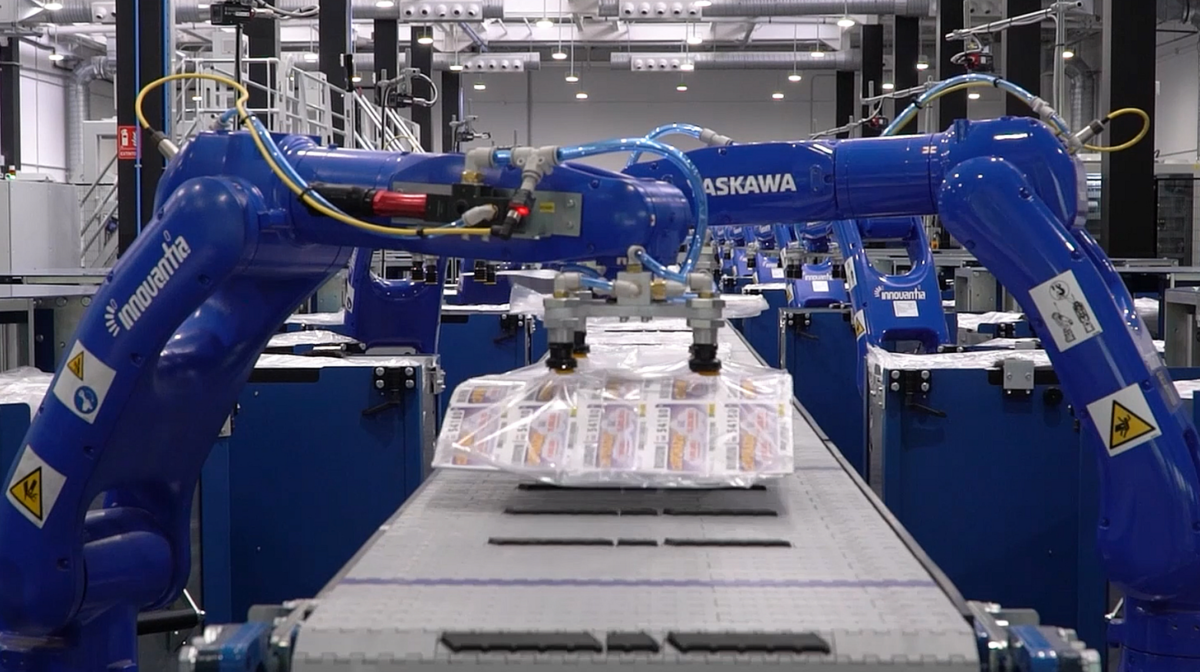
How did the decision to implement this specific automation solution come about?
The solution offered by Yaskawa fitted at all times with the type of processes that were required to meet the demand of our client, with the support of the technology to generate these processes. All of this was based on the roadmap drawn up between Innovantia® and ONCE as part of a previous automation study.
The following are some of the criteria that helped us to choose Yaskawa as the partner of choice for the implementation of our client's automated preparation.
Simplicity of implementation. The choice of Yaskawa as a partner for these technologies was due to its ease of implementation.
Simplicity of operation. The fundamental premise of the roadmap was that the selected automation solutions had to be flexible, easy to use and control, and at the same time our technicians had to have the necessary training and documentation on the equipment deployed.
Structure. We were looking for a reliable and scalable solution that would provide the large number of automated processes with greater stability, and which, when the time came, would facilitate implementation both physically and in cloud services.
Scalability. Scalability was another key factor in our decision to go with Yaskawa. We demanded an efficient and operational solution, even in this case when a large number of robots and automated processes were required to run simultaneously. Another decisive feature was the possibility of integrating commercial solutions from the market provided by third parties so that they could easily participate in the automation process.
Maintenance and support from our partner. Our business relationship with Yaskawa as an official integrator gives us the security of having stable, low-maintenance solutions and good manufacturer support, both in planning scenarios and during implementation in demanding operating environments.
Could you describe the implementation process, including any challenges you faced during this period?
The implementation, and the first challenge, started with understanding and studying the customer's automation requirements, identifying the specific needs of the solution required for ONCE.
In this sense, the challenge of automating the Central Preparation Unit was to handle weekly the elements and media necessary to meet the demand of around 36,000 points of sale, reaching up to more than 400,000 media, duly identified and read, determining the absolute traceability of the order, from its printing to its reception at the corresponding sales point.
Up to 8 versions of the preliminary project were produced, which included detailed proposals with formats, cycles and functionalities that the line should have. These documents had to be validated by all ONCE and INNOVANTIA® departments in order to transfer knowledge between both parties and study the best practices to be implemented in the final solution.
This made it possible to improve and optimise steps of the manual process prior to the implemented solution. The project led by INNOVANTIA® started even before the development of the project itself, advising and coordinating a consortium of different architecture and construction companies, IT companies, and more than 50 different suppliers of machinery and industrial equipment.
Once the data was defined, the main design challenges were:
The physical cycle time of a single package had to be less than 4.35 seconds. The design was carried out entirely in 3D, using YASKAWA simulation software, which allowed us to know ranges and cycles. The results of these simulations were then validated during manufacture.
The processing time of the large volume of data had to be as short as possible in order to maximise the cycle time of the machines. This required processing the data in tenths of a second, and the most powerful automaton on the market at the time was chosen.
Having achieved this millisecond processing in reading and writing on a physical server, in order to avoid the operational problems that could arise when using a server of this type, a virtual server was developed with BackUp in the cloud. Access to this server made it necessary to connect to the installation via VPN, ensuring the integrity of the information and service of the IT security architecture at all times.
An absolute traceability system was developed with readings and checks of each of the 200,000 supports, by means of readers, vision systems, label printing systems, etc. This ensures total quality control in order processing, with a complete check of what has been processed by the installation. This was one of the main reasons for ONCE to automate, going from having errors in the processing of manual packages to 0% after the implementation of the robotisation solution for the line.
The implementation was developed based on Industry 4.0 and IoT theories, with the visualisation of production data in real time, as well as yields and alarms from any device connected to the internet such as computers, tablets or smartphones. This has enabled ONCE and INNOVANTIA® to help evaluate, debug and optimise processes throughout the supply chain.
The last of the challenges was the implementation. The implementation process took months and was carried out by incorporating the 33 existing logistics centres into the robotised installation one by one. For this purpose, traceability was checked week by week, from the computerised generation of the order to the activation of the support by each lottery retailer at their POS.
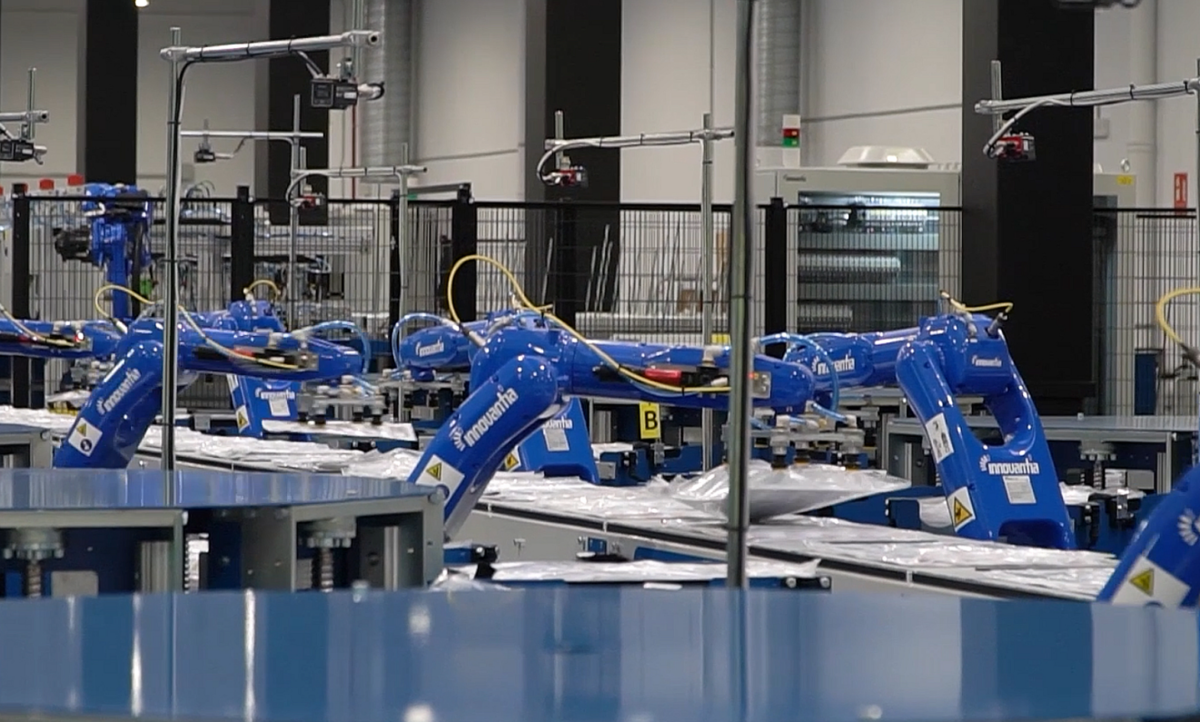
The result has been an installation with:
- 22 robots, which do the handling of passive gaming products or coupons, instant lottery or gaming books and consumable supports.
- 2 depalletising and palletisingrobots.
- 3 delta-type robots (impressive for their speed of movement and wingspan due to the high inertia generated) for pre-preparation of lottery game books and paper rolls for the retailers' POS terminals.
- 96 automated loaders for passive gaming products, plus 8 loaders for the management of consumable media (such as advertising, betting slips, coupon holders, etc.), housed in 13 automatic loaders.
- 216 loader transport trolleys to ergonomically manage the loading and unloading of the 848 loaders.
- 3 autonomous mobile robots (AMR), to transport trolleys from the printing plant to the installation for the preparation of orders, as well as from the orders placed in the installation to the warehouse or loading dock.
This equipment is completed with more than 300 metres of conveyor belts, labellers, bagging machines, print heads, sensors, artificial vision cameras, servomotors, enconder, variators, automatons, etc.
How was the collaboration with Yaskawa during the process?
Innovantia®, which had done previous work on the regeneration of ONCE's printing presses successfully, was presented together with Yaskawa as a solid and reliable equipment proposal.
During the project, in the process of collaborating with Yaskawa as an equipment proposal, we experienced a good synergy that facilitated our operations. First of all, the ease of access to technical data of the robots allowed us to understand and choose in a dynamic way the capabilities and technical specifications needed for our project.
The availability of downloadable CAD models for simulations was a valuable resource when choosing the equipment and allowed us to visualise and analyse precisely how the robots would be integrated into our working environment prior to actual implementation.
In fact, one of the highlights of our collaboration was Yaskawa's direct support in performing robot motion simulations, considering both cycle time and required ranges. This assistance provided us with in-depth understanding and solid confidence in choosing and ensuring the effectiveness of our solution.
Another important point to note is that our project involved the simultaneous coordination of 30 robots.
We relied on Yaskawa's expertise and capabilities were critical. They provided us with expert guidance to handle this complex task efficiently and effectively.
In addition, they provided expert advice on how to transition from 4 to 6-axis robots in palletising / depalletising, which significantly improved the capacity of both zones by increasing management in both cells by extending the handling capability and accuracy in the process.
In summary, the partnership with Yaskawa was critical to the success of our project, thanks to their commitment to innovation, quality and continuous support at all stages of the process.