Unser umfangreiches Robotersortiment bietet neben anwendungsbezogenen Varianten wie Schweiss-, Palettier-, Lackier- und Handling-Roboter auch Modelle für Labor- und Reinraumapplikationen sowie schlüsselfertige automatisierte Schweißsysteme höchster Qualität.
Vollautomatisches Schweißen kleiner Losgrößen
Roboterschweißzelle mit eingebauter Flexibilität
Der weltweit führende Werkstattausrüster MAHA hat am Stammsitz in Haldenwang eine Roboterschweißanlage in Betrieb genommen, die in Sachen Flexibilität Maßstäbe setzt.
Nach einjähriger Einsatzdauer sind bereits Programme für über 150 Schweißbaugruppen hinterlegt – Tendenz weiter steigend.
MAHA zählt zu den Weltmarktführern in der Werkstatt- und Kraftfahrzeugprüfausrüstung. Das 1969 von Winfried Rauch im Allgäu gegründete Unternehmen entwickelte sich rasch zum Global Player, der heute über 1.200 Mitarbeiter weltweit beschäftigt und mit 150 Vertretungen sowie 17 eigenen Niederlassungen international präsent ist.
Am heimischen Standort Haldenwang produzieren rund 750 Beschäftigte die komplette Bandbreite an Werkstattausrüstung von Prüfständen über Fahrzeug-Hebebühnen bis hin zu diversen Prüfgeräten für Pkw, Nutzfahrzeuge, Motorräder und Spezialfahrzeuge. Werkstätten und Prüforganisationen in aller Welt schätzen die überlegene Qualität der Produkte, die sich durch Langlebigkeit und Zuverlässigkeit auszeichnen.
Kleine Losgrößen zwischen 10 und 100
Was dieses Qualitätsversprechen für die Produktion bedeutet, bringt Erich Schmölz, Abteilungsleiter Roboterschweißen bei MAHA, auf den Punkt: „Wir müssen auf der Roboteranlage Schweißbaugruppen in kleinen Losgrößen und in absolut reproduzierbarer Qualität schweißen. Bei unseren Hebebühnen beispielsweise, die wir im LKW-Bereich mit einer maximalen Traglast von bis zu 60 Tonnen anbieten, hängen Menschenleben von der korrekten Ausführung der Schweißnähte ab. Entsprechend hoch sind die Anforderungen an die Schweißergebnisse, die je nach Relevanz entsprechenden Qualitätsprüfungen unterzogen werden.“
Höchste Qualität bei gleichzeitig maximaler Flexibilität – diese Quadratur des Kreises gelingt MAHA mit einer wegweisenden Roboterschweißanlage, die die Schweißexperten von YASKAWA in enger Abstimmung mit den MAHA-Verantwortlichen schlüsselfertig projektiert, realisiert und in Haldenwang in Betrieb genommen haben.
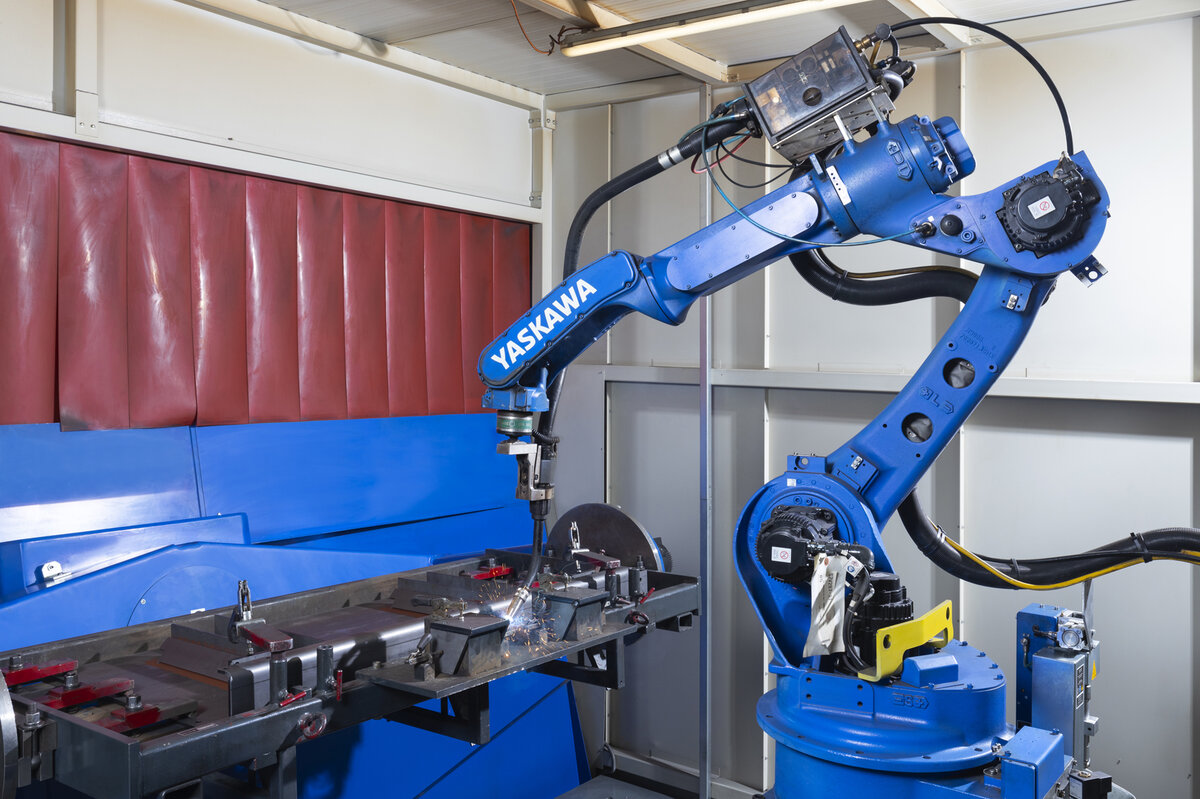
Roboterschweißanlage schlüsselfertig konzipiert und realisiert
„Die komplette Zelle besteht überwiegend aus Standardkomponenten von YASKAWA, wobei der sechsachsige Hochgeschwindigkeits-Schweißroboter MOTOMAN MA2010 mit der DX200 Steuerung und der Fünfachs-Servopositionierer R2C mit seinen zwei Stationen für simultanes Schweißen und hauptzeitparalleles Bestücken die eigentlichen Flexibilitätsgaranten darstellen“ betont YASKAWA-Salesmanager Roland Hermann.
Was auffällt beim Blick auf die Zelle, ist die um etwa 15 Grad geneigte Anordnung des Positionierers, die es dem Bediener erlaubt, die Teile auf der Beladeseite möglichst einfach und ergonomisch einlegen und spannen zu können. Auch der Wechsel der Vorrichtungen – so heißen die Aufnahmen für die entsprechenden Teilevarianten – wird durch diesen konstruktiven Kniff erleichtert, was die Umrüstzeiten auf fünf bis zehn Minuten schrumpfen lässt.
Dreht der Positionierer um 180 Grad in den Arbeitsbereich, führt die Neigung dort zu einer erhöhten Arbeitsposition für den Schweißroboter, der deshalb auf einem Sockel montiert ist. Weiterer Vorteil dieser Position ist die hervorragende Zugänglichkeit des Roboters. Insgesamt erlauben die fünf NC-Achsen des R2C-Positioniers und die sechs Achsen des Roboters, die die DX200 Steuerung vorbildlich synchronisiert, eine stets perfekte Schweißposition in Wannenlage.
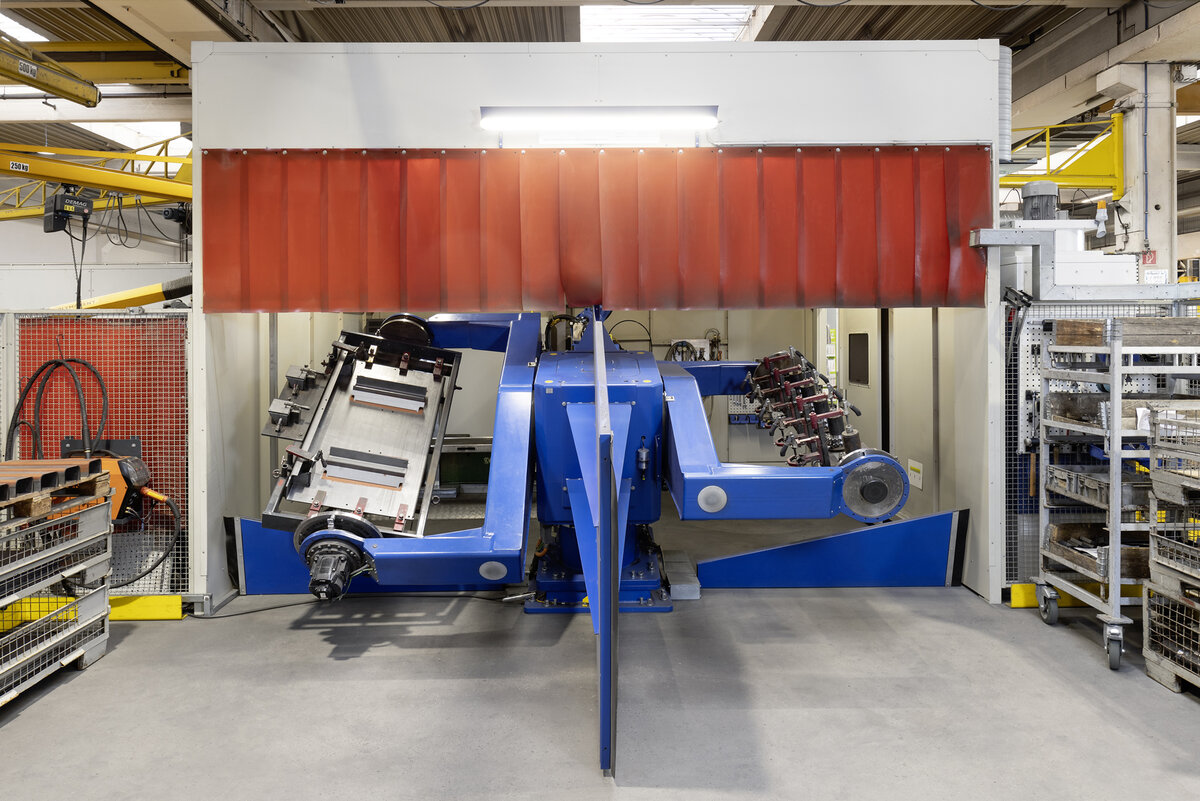
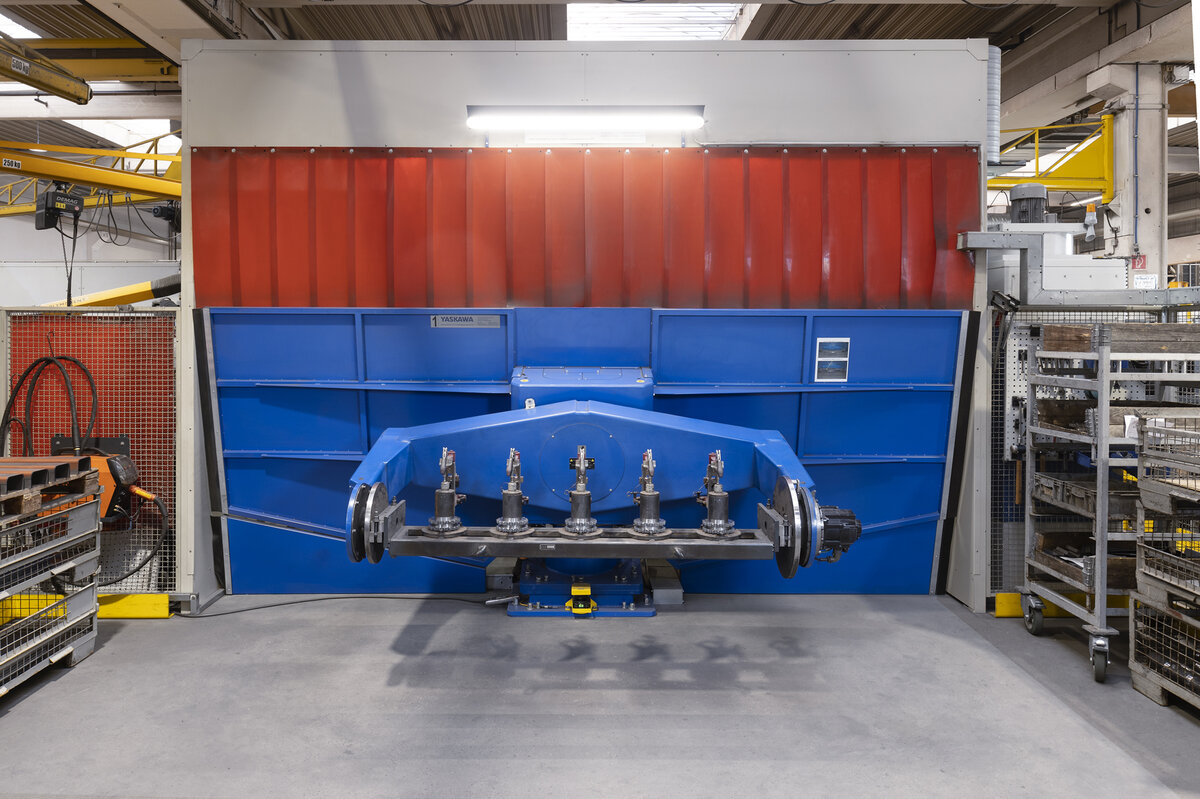
Offline Programmierung steigert Produktivität
Was Schweißfachmann Schmölz besonders schätzt an der Anlage, ist die Möglichkeit der Offline-Programmierung: „Über die CAD-Daten können wir jede Schweißbaugruppe hauptzeitparallel offline programmieren, Schweißzeiten exakt berechnen, Fügefolgen im Sinne des geringsten Verzugs festlegen, Kollisionen vermeiden und vieles mehr. Die Offline-Programmierung führt gerade bei unseren Einsatzbedingungen mit vielen Kleinteilen zu signifikanten Produktivitätssteigerungen.“
Oftmals werden auf der Anlage zwei unterschiedliche Baugruppen im Wechsel geschweißt – mit dem 2-Stationen-Positionierer ist auch das kein Problem. Es ist lediglich darauf zu achten, dass die Einlegezeiten kürzer als die Schweißzeiten sind, denn Stillstandszeiten des Roboters sind bei MAHA so gar nicht gefragt. Deshalb hat man sich auch für den MOTOMAN MA2010 entschieden. Der Sechsachser ist als unverwüstlich bekannt bekannt und verrichtet seine Arbeit auch im Schichtbetrieb rund um die Uhr immer mit der erforderlichen Bahngenauigkeit. Die Maschine liefert prozesssichere Schweißergebnisse Teil für Teil ohne jede Abweichung von den vorgegebenen Toleranzen. Dabei geht der schlanke Roboter dynamisch ans Werk und sorgt so für einen maximalen Output. Seine Reichweite beträgt bei 10 kg Traglast beachtliche 2010 mm.
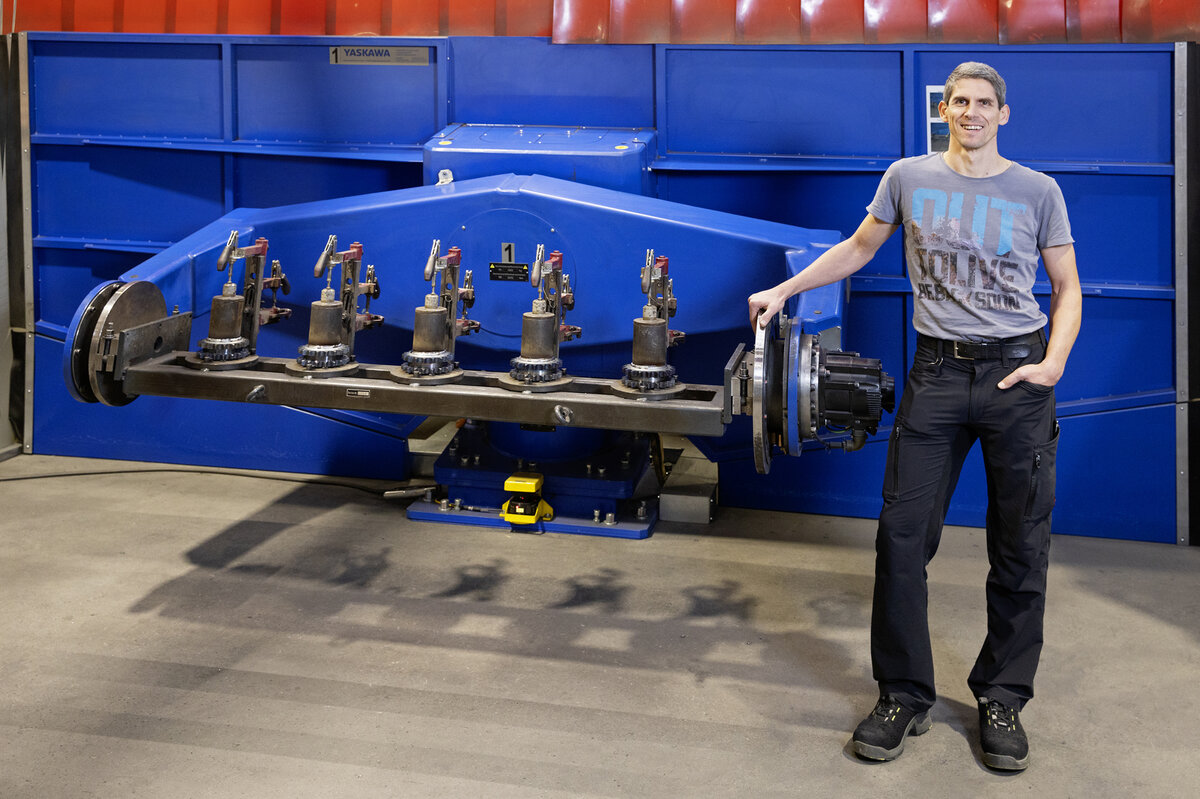
Zuverlässigkeit und Know-how begünstigen Entscheidung
Natürlich haben sich die MAHA-Verantwortlichen vor der Investition in diese Anlage auch bei anderen Herstellern umgesehen, sind dann aber doch wieder bei YASKAWA gelandet. Ein Grund dafür ist sicherlich der Tatsache geschuldet, dass im Werk Haldenwang MOTOMAN Schweißroboter im Einsatz sind, die bereits seit 22 Jahren zuverlässig ihren Dienst versehen.
Aber neben diesem beeindruckenden Qualitätsbeweis sprachen viele weitere Gründe für YASKAWA. Die Wichtigsten darunter bringt Erich Schmölz auf den Punkt: „YASKAWA hat unglaublich viel Erfahrung und kann Schweißanlagen exakt nach Kundenwunsch schlüsselfertig konzipieren und unter Verwendung vieler eigener Standardkomponenten realisieren. Von diesem Know-how profitieren wir ebenso wie vom vorbildlichen Service und der sprichwörtlichen Zuverlässigkeit.“ Da dürfen die reibungslose Integration der Schweißanlage in die Produktion sowie der seither störungsfreie Betrieb als normal gelten.
Top-Performance zieht weitere Investition nach sich
Auch die Bediener der Anlage sind von deren Performance begeistert. Sie schätzen vor allem die hervorragende Zugänglichkeit des großzügig gestalteten Einlegebereichs der Anlage, der über Bodenscanner, Lichtschranken und Schutzgitter abgesichert ist. Hier ist Platz genug, um Teile mit dem Hubwagen oder dem Gabelstapler bereitstellen zu können. Auch die einfache und komfortable Bedienung der Anlage erleichtert die tägliche Arbeit. Dazu gehört auch ein erweiterter Blendschutz am Positionierer, durch den sich ein komplett geschlossener Schweißbereich ergibt. Hier sorgt eine leistungsfähige Schweißrauch-Absauganlage dafür, dass die Hallenluft unbelastet bleibt.
Alles in allem haben sich die hohen MAHA-Erwartungen an die Anlage im Praxisalltag uneingeschränkt erfüllt. „Mit dieser Anlage ist es uns gelungen, unser vorrangiges Ziel, die Flexibilität von Schweißprozessen mit kleinen Losgrößen signifikant zu erhöhen, perfekt umzusetzen. Die Produktivität der Anlage ist somit trotz eines immensen Teilespektrums auf Topniveau, weshalb die Planungen für eine zweite, baugleiche Anlage bereits weit fortgeschritten sind“, resümiert Erich Schmölz.
Text: Ralf Högel
Kontakt für Leseranfragen:
Tel. +49-8166-90-0
Fax +49-8166-90-103