Unser umfangreiches Robotersortiment bietet neben anwendungsbezogenen Varianten wie Schweiss-, Palettier-, Lackier- und Handling-Roboter auch Modelle für Labor- und Reinraumapplikationen sowie schlüsselfertige automatisierte Schweißsysteme höchster Qualität.
Zwei Bearbeitungsmaschinen mit großer Autonomie verkettet
Verkettete Magnesiumbearbeitung zuverlässig automatisiert
Magnesium ist das Leichtbaumetall mit der niedrigsten Dichte, die bei rund einem Viertel der Dichte von Stahl und rund 35% unter der von Aluminium liegt. Wenn man in der Fachliteratur nachschlägt, erfährt man, dass niedrige Zerspankräfte bei der Bearbeitung charakteristisch sind, was wiederum einen geringen Werkzeugverschleiß zur Folge hat.
Abgebildet auf die Automation eines Zerspanungsprozesses bedeutet das sehr hohe Anforderungen an die Zuverlässigkeit und technische Verfügbarkeit der Automation sowie an die Werkstückautonomie.
Auf den Punkt gebracht: Die Anlage muss lange zuverlässig und ohne Störung laufen und dabei einen großen Werkstückpuffer für Roh- und Fertigteile bieten, der einerseits jederzeit nachgefüllt und entleert werden kann, aber auch ausreichend Kapazität bieten muss um ohne Bedienereingriff eine Nacht oder ein Wochenende durchzulaufen.
Im konkreten Fall erfolgt die Bearbeitung der beiden Werkstückseiten nacheinander auf zwei Maschinen, auf dem ersten Bearbeitungszentrum vierfach, auf der zweiten Maschine einzeln. Gleichzeitig soll der Bearbeitungsraum der Maschinen für Rüstvorgänge und Anlaufteile händisch zugänglich sein. Als Zusatzprozess soll die Kennzeichnung der Werkstücke nach erfolgter Bearbeitung mit einem Data Matrix Code in den Automatisierungsablauf integriert werden.
Die Firma Schwab CNC Metallbearbeitung fertigt seit dem Jahr 2010 hochqualitative Fräs- und Drehteile für diverse Branchen.
Gemäß der Unternehmens-Philosophie „Professionelle Betreuung während des gesamten Produktlebenszyklus – von der Prototypenentwicklung über die Serienfertigung bis hin zum Ersatzteil“ werden sowohl einzelne Prototypen als auch größere Serien im Bereich Aluminium- und Magnesiumdruckguss gefertigt.
Zum Leistungsspektrum des Unternehmens mit Sitz in Rot am See im Landkreis Schwäbisch Hall, dem fränkisch geprägten Nordosten Baden-Württembergs, gehört darüber hinaus die ausführliche technische Beratung des Kunden vor und während dem Projekt. Das Familienunternehmen mit 14 Mitarbeitern wird von Vater Reiner und Sohn Markus Schwab geführt.
Entwickelt und realisiert wurde die Automation als Turnkey-System von der EGS Automatisierungstechnik GmbH aus Donaueschingen im Schwarzwald-Baar-Kreis. Das Unternehmen ist seit 1996 im Bereich der industriellen Automation aktiv und setzt dazu seit 1999 Industrieroboter ein. Die Kunden profitieren dabei von der Erfahrung aus mehr als 1750 installierten Robotern bis zum Zeitpunkt der Inbetriebnahme der beschriebenen Anlage im Jahre 2019.
Bei dem Werkstück "Actuator Housing" handelt es sich um ein Gehäusebauteil aus Magnesium für Lenkgetriebe von Kraftfahrzeugen, das bereits seit längerer Zeit im Hause Schwab bearbeitet wird. Eine kräftige Stückzahlerhöhung der Abrufe, die eine Jahresausbringung von bis zu 250.000 Teilen erfordern, war der wesentliche Grund für eine Automatisierung der Bearbeitung der Teile. Da das Unternehmen auch mit dem Fachkräftemangel zu kämpfen hat, werden die Mitarbeiter, die bisher den Prozess händisch bedient haben, für andere Tätigkeiten frei, wo sie dringend gebraucht werden.
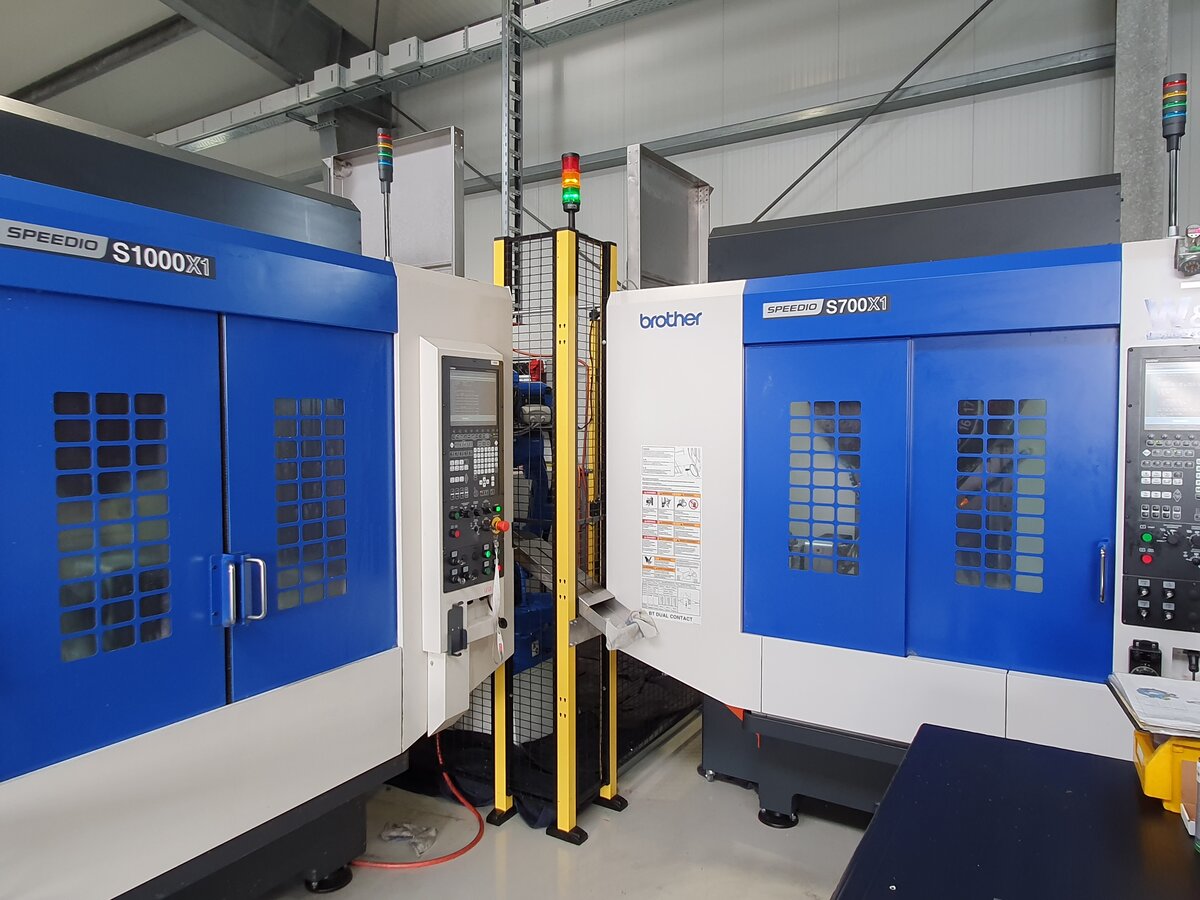
Ausgangspunkt für den Automatisierungsprozess war ein vorhandenes Bearbeitungszentrum Brother Speedio S1000, in dem eine Seite der Werkstücke in eine 4fach-Aufspannung bearbeitet werden. Die vorhandene Spannvorrichtung, in die die Bauteile bisher händisch eingelegt wurden, sollte mit möglichst wenigen Modifikationen automatisch bestückt werden. Die Bearbeitungszeit und der Werkstückwechsel liegen in Summe bei circa sechs Minuten für vier Teile, was auch die taktzeitbestimmende Vorgabe für die Automation war. An der Maschine wurde eine seitliche Beladeluke nachgerüstet, die sowohl in den Sicherheitskreis der Maschine als auch in den Sicherheitskreis der Roboterzelle eingebunden wurde.
Bei der Auswahl des passenden Roboters spielte die erforderliche Reichweite eine entscheidende Rolle. Um alle Positionen auf der Vorrichtung zu erreichen, muss der Roboter relativ weit in die Maschine eintauchen. Verbunden mit der erforderlichen Präzision beim Handhaben und Einlegen der Teile und der notwendigen hohen Verfahrgeschwindigkeit fiel die Wahl auf einen Industrieroboter MOTOMAN GP25 mit einer YRC1000-Steuerung. Dass Roboter von Yaskawa auch unter den schwierigen Umgebungsbedingungen in Werkzeugmaschinen über viele Jahre zuverlässig funktionieren, haben die zahlreichen Installationen von EGS in diesem Anwendungsbereich bewiesen.
Die zweite wichtige Vorgabe war die Autonomie der Automationsanlage. Die Anlage sollte möglichst 12 Fertigungsstunden autonom fertigen können. Dafür muss eine Speicherkapazität für 480 Rohteile und 480 Fertigteile vorhanden sein. Die Bauteilabmessung des geometrisch komplexen Werkstücks betragen grob 145x135x50mm, das Gewicht liegt bei rund 200 Gramm. Für diese voluminöse Teilebevorratung und Bereitstellung wurde der SUMO Ecoplex2 von EGS eingesetzt. Es handelt sich dabei um ein Palettiersystem für Werkstückträger bis zu einer Größe von 600x400mm. Die Werkstückträger werden gestapelt bevorratet, depalettiert dem Roboter zur Teileentnahme zur Verfügung gestellt und nach Befüllung mit Fertigteilen zurück palettiert. In der verwendeten speziellen Ausführung mit Zu- und Abführbändern beträgt die Kapazität sechs Werkstückträgerstapel für Roh- und Fertigteile. Diese große Autonomie ist durch eine spezielle, verstärkte Bandausführung möglich.
Als Werkstückträger wurden handelsübliche, automatisierungsgerechte und stapelfähige Kunststoffbehälter ausgewählt. Die werkstückspezifischen Inlays, in denen die Bauteile exakt positioniert aufgenommen werden, wurden von EGS konstruiert und von Schwab mit den eigenen Fertigungskapazitäten hergestellt. Die richtige Gestaltung von Werkstückträgern ist für die Zuverlässigkeit der späteren Automation elementar und gehört daher in die Verantwortung eines Spezialisten.
Eine ebenfalls wichtige Kernkomponente ist die Greiftechnik. Hier kommen Greifmodule des langjährigen Lieferanten Zimmer Group zum Einsatz, die sich in zahlreichen realisierten Anwendungen bei der Automation von Werkzeugmaschinen auch unter widrigsten Bedingungen bewährt haben.
Beim Engineering und der Fertigung der eigentlichen Greiferfinger, sowie der geometrisch optimalen Positionierung der Greifmodule an der Roboterhand im Hinblick auf genaue Positionierung, sicheren Griff und optimale Zugänglichkeit in allen Greifpositionen kommt die langjährige Erfahrung von EGS zur Geltung.
Die zweite Seite der Werkstücke wird in einer zweiten Maschine bearbeitet, einer Brother Speedio S700. Auch hier erfolgt die automatische Beladung seitlich durch eine spezielle Beladeluke. Die Bearbeitung der zweiten Seite ist weitaus weniger umfangreich und dauert daher deutlich kürzer und erfolgt hier einzeln.
Da die erste Maschine für den Anlagentakt bestimmen ist, müssen aus dieser immer direkt nach Bearbeitungsende die vier bearbeiteten Werkstücke entnommen und vier neue Rohteile eingelegt werden. Zur Zwischenablage für die Halbfertigteile dient eine kombinierte Ablage- und Wendestation mit vier Werkstückaufnahmen. Hier legt der Roboter die Bauteile auf und holt sie gewendet zur Beladung der zweiten Maschine wieder ab.
In beiden Maschinen werden die Bauteile nach der Bearbeitung und vor dem Entnehmen mittels einer Blasdüse, die am Roboterwerkzeug angebracht ist, weitestgehend vom Kühlschmiermittel befreit, um eine unnötige Verschleppung zu vermeiden.
Nach erfolgter Bearbeitung muss auf jedem Bauteil noch ein Datamatrix Code aufgebracht werden. Dazu kommt ein Kennzeichnungslaser von Koenig &Bauer Coding zum Einsatz. Als Anlagenhersteller ist EGS Automatisierungstechnik für die Einhaltung der Lasersicherheit verantwortlich. Dies wird durch entsprechende Schutzeinrichtung am Greifwerkzeug realisiert sowie entsprechender Sensorik, die sicher überwacht, dass der Laser nur arbeiten kann, wenn die Schutzabschrankung den Kennzeichnungsbereich sicher abdeckt. Während der Beschriftung wird das Werkstück vom Roboter sicher und genau in Position gehalten, die entstehenden Dämpfe werden abgesaugt. Der aufgebrachte Code enthält die Information zum Fertigungsdatum sowie eine fortlaufende Nummer. Nach erfolgter Kennzeichnung legt der Roboter das Fertigteil zurück in einen Werkstückträger, der im Palettiersystem SUMO Ecoplex2 auf einen Fertigteilstapel abpalettiert wird und dort vom Bedienpersonal je nach Verfügbarkeit entnommen werden kann. Die Werkstückträgerstapel der Roh- und Fertigteile werden an einer Bedienseite der Anlage aufgestellt und entnommen. Es besteht die Möglichkeit diese an anderer Stelle vorzubereiten und von einem speziellen Wagen ergonomisch auf das Band überzuschieben. Die Anlage läuft grundsätzlich bis zu 12 Stunden autark, es können aber auch jederzeit zwischendurch vorhandene Fertigteile entnommen oder neue Rohteile eingebracht werden.
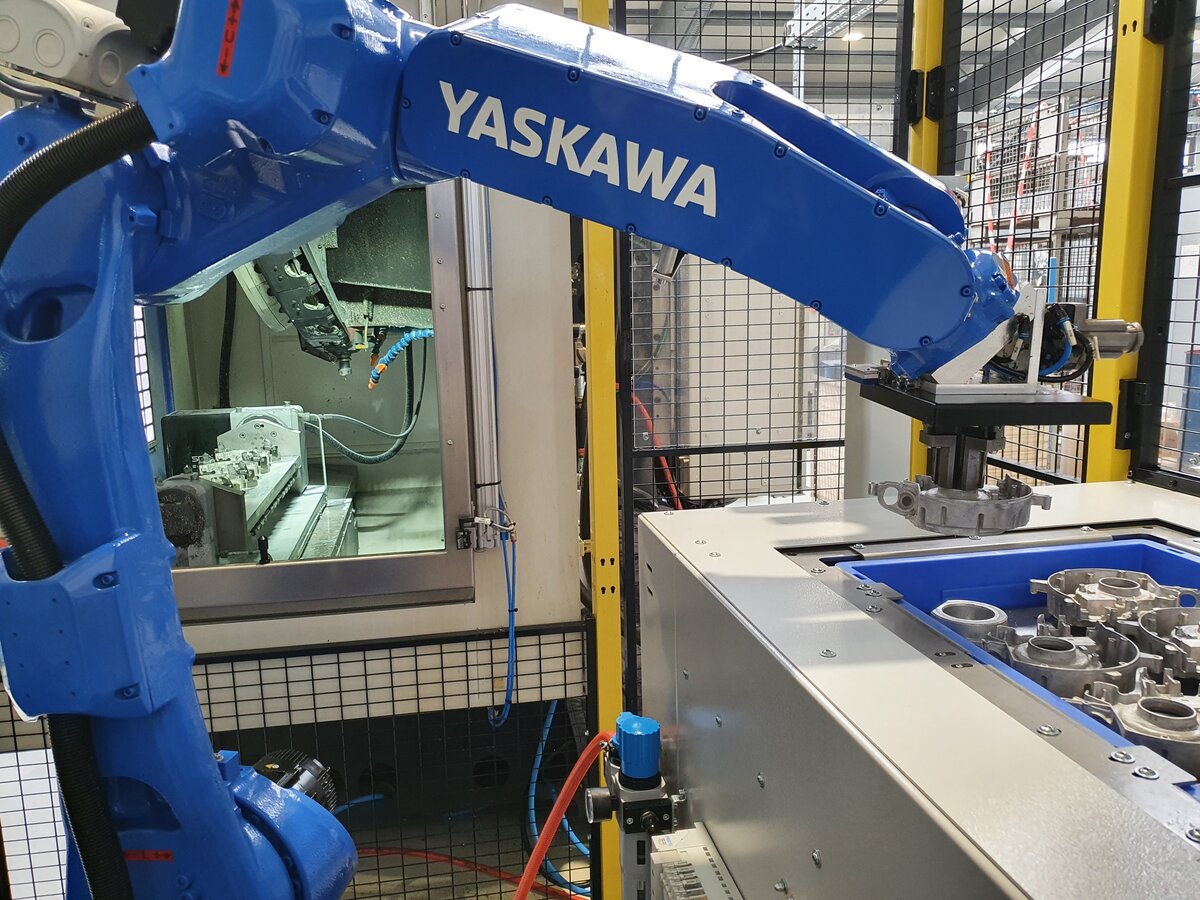
Alle Abläufe werden von der Robotersteuerung YRC1000 gesteuert und die gesamte Anlage über das leichte und ergonomische Bedienhandgerät des Roboters über eine spezielle Oberfläche bedient. Die elektrischen Schnittstellen zu den beiden Maschinen wurden, nach vorheriger schneller und unbürokratischer Abstimmung zwischen EGS und dem Maschinenhersteller, auf Basis von Profinet realisiert. In einer zweitägigen Bedienerschulung wurde das Bedienpersonal in die Handhabung der Anlage eingewiesen. Obwohl es bei Schwab CNC Metallbearbeitung vorher keinerlei Erfahrung mit Robotik gab, ist man mit diesen Voraussetzungen ohne Probleme in der Lage die Anlage zu bedienen und den Roboter manuell zu verfahren.
Die vereinbarte Anlagentaktzeit wurde sogar leicht unterschritten, so dass aktuell der Roboter schneller ist als die taktzeitbestimmende erste Maschine.
So fällt das Fazit von Junior-Chef Markus Schwab rundum positiv aus: "Wir bedanken uns bei EGS für die reibungslose Installation und überaus schnelle Inbetriebnahme der Anlage. Durch den SUMO Ecoplex2 haben wir die Chance auch in Zeiten von Fachkräftemangel am Markt zu bestehen und unseren Kunden die gewünschte Sicherheit und Flexibilität zu bieten."
Bildquelle: EGS Automatisierungstechnik GmbH
Autor und Kontakt:
EGS Automatisierungstechnik GmbH
Heiko Röhrig, Leiter Vertrieb u. Marketing
Fon +49 771 898 606 27
Kontakt für Leseranfragen Yaskawa:
Tel. +49-8166-90-0
Fax +49-8166-90-103